Rohre biegen mit Cyberbrille
Maschinen bedienen leichtgemacht: Ein Forschungsverbund der Uni Siegen hat ein System entwickelt, das mit moderner Technik Maschinenbediener in der Industrie unterstützt und Wissen von erfahrenen Mitarbeitern weitergibt.
Man stelle sich einmal vor, beim Aufbau eines Möbelstücks
würde einem eine intelligente Brille mit einer Art
Hologramm Schritt für Schritt zeigen, was zu tun ist. Von
der Wahl des Werkzeugs bis zum richtigen Einsatz.
Unverständliche Bedienungsanleitungen gehörten der
Vergangenheit an und selbst handwerklich unbegabte Menschen
dürften einsturzsichere Regale aufbauen können. Die
Ergebnisse eines Forschungsprojekts der Universität Siegen
könnten ähnliches in Zukunft ermöglichen – nur stehen nicht
Hobby-Heimwerker im Mittelpunkt, sondern Maschinenbediener
in Unternehmen.
Was passiert mit dem Wissen von erfahrenen Fachkräften,
wenn diese aus dem Berufsleben ausscheiden? Diese Frage war
der Ausgangspunkt, als Projektleiter Dr.-Ing. Christopher
Kuhnhen und sein Team des Forschungsverbunds im April 2016
die Arbeit aufgenommen haben. Die Wissenschaftler wollten
Wege finden, wie die Expertise nahtlos an jüngere Kollegen
weitergegeben werden kann und wie dies mit Methoden der
oftmals noch abstrakten Industrie 4.0 realisierbar ist.
„Wir können jetzt etwas vorzeigen, das auch für
mittelständische Unternehmen konkret nutzbar sein und die
Arbeit erleichtern wird“, freut sich Prof. Dr.-Ing. Bernd
Engel, Inhaber des Lehrstuhls für Umformtechnik.
In Kooperation mit dem Lehrstuhl für Wirtschaftsinformatik
und Neue Medien um Leiter Prof. Dr. Volker Wulf, dem
Siegener Mittelstandsinstitut (SMI) und Betrieben aus der
Region ist ein System entstanden, das Maschinenbediener mit
Hilfe einer Cyberbrille bei ihrer täglichen Arbeit
unterstützen und Arbeitsabläufe deutlich verkürzen soll. Im
mit EU-Mitteln geförderten Projekt stand ein Biegeprozess
im Mittelpunkt, das System lässt sich aber auch auf andere
Branchen wie zum Beispiel Kunststoff oder Zerspanung
übertragen. So wurden die Entwicklungen bereits diversen
Unternehmen aus der Region vorgestellt. Die Reaktionen
seien überragend gewesen, berichtet Kuhnhen.
Der eigentliche Arbeitsvorgang gliedert sich in zwei
Prozesse: einen statischen und einen dynamischen. Bevor die
Maschine das Rohr den Wünschen des Bedieners entsprechend
biegen kann, muss sie gerüstet, also mit Werkzeugen
bestückt werden. Der Maschinenbediener setzt sich die
HoloLens, eine sogenannte Mixed-Reality-Brille auf. Blickt
der Anwender auf die reale Maschine, erscheint dort eine
virtuelle Nachbildung. Über die Brille wird nun jeder
Arbeitsschritt nach und nach eingeblendet. Zudem können per
Fingerzeig Videos abgespielt werden, die den Vorgang
erläutern. Durch diese Anweisungen könnten zum Beispiel
auch unerfahrenere Mitarbeiter problemlos Maschinen rüsten.
„Es ist eine Art Navigationsgerät für Maschinenbediener“,
so Kuhnhen. Wichtiger Faktor: Die Dauer des Rüstprozesses
werde so um bis zu 50 Prozent verkürzt.
Im zweiten Schritt geht es um die Feinjustierung. Beim von
den Forschern angewendeten „Rotationszugbiegen“ müssen
sieben verschiedene Achsen eingestellt werden. Um ein
perfektes Ergebnis zu bekommen ist entweder viel Erfahrung
erforderlich – oder ein langes Tüfteln an den
Einstellungen. Das von der Forschungsgruppe entwickelte und
vom Hard- und Softwarespezialisten „Lachmann und Rink“ aus
Freudenberg umgesetzte Programm schlägt dem
Maschinenbediener die bestmöglichen Parameter vor. Damit
das funktioniert, haben die Wissenschaftler erfahrenen
Mitarbeitern des Hilchenbacher Unternehmens „Westfalia
Metallschlauchtechnik“ mehrere Wochen lang auf die Finger
geschaut und Interviews mit ihnen geführt. Ihr Wissen
fließt somit direkt in das Programm ein und wird
weitergegeben. Zudem ist das Programm lernfähig: Produziert
der Maschinenbediener ein Rohr mit Falten, erhält er
aufgrund der Erfahrungen bei ähnlichen Problemen
Vorschläge, die die Fehler beheben könnten. Es wird
überprüft, welche Einstellungen bei welchen Problemen zum
Erfolg geführt haben. Letztendlich soll ein enormer
Zeitgewinn bei gleichzeitig hoher Qualität des Produktes
stehen.
Prof. Engel hofft, dass den Unternehmen mit dieser
Entwicklung auch ein wenig die Angst vor dem Begriff
Industrie 4.0 genommen werden kann. „Wir wollen nicht den
Menschen durch Maschinen ersetzen, sondern Prozesse mit den
Menschen weiterentwickeln.“
Hintergrund
Das Projekt mit dem Titel „Cyberrüsten 4.0“ hat einen
Gesamtumfang von 2,6 Millionen Euro. Auf die Universität
Siegen entfallen fast 1,5 Millionen Euro, wovon 90 Prozent
vom Fördermittelgeber EFRE (Europäischer Fonds für
regionale Entwicklung) getragen werden. Beteiligt waren
mehrere Partner: Lehrstuhl für Umformtechnik (Univ.-Prof.
Dr.-Ing. Bernd Engel, Dr.-Ing. Christopher Kuhnhen
(Projektleiter/Verbundkoordinator), M. Eng. Linda
Borchmann); Lehrstuhl für Wirtschaftsinformatik und Neue
Medien (Univ.-Prof. Dr. Volker Wulf, M. Sc. Sven Hoffmann,
Dr. Fabiano Pinatti de Carvalho); Siegener
Mittelstandsinstitut SMI (Prof. Dr. Marcus Schweitzer, M.
Sc. Nils Darwin Abele); Lachmann & Rink GmbH,
Freudenberg (Dipl.-Ing. Stefan Thilo, Dr. Matthias Hebbel,
Eric Behme, B. Sc. Bedrettin Aslan); Westfalia
Metallschlauchtechnik GmbH & Co. KG, Hilchenbach (Dr.
Oliver Selter, Sascha Sckudlarek, Marcus Hupertz).
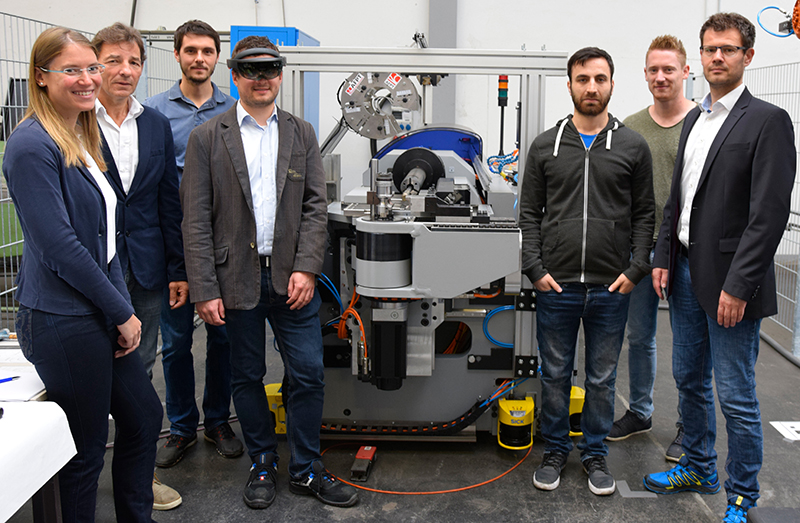